|
Fluid Bed Coating
|
|
|
|
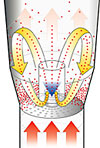 |
Film coating, lipid/hot melt coating.
Specific manipulation of the particle surface
characteristics. Protection of the product against moisture, light, air,
...
Specific manipulation of the way in which the particle dissolves, the
decomposition or the release of active ingredients.
Coating of microparticles, granules, pellets or tablets.
|
|
|
Process advantages
Uniform, continuous product coating. Aqueous or organic coatings can be
applied. Coating and drying take place in one machine. In terms of Total Containment, the coating process and
the filling and emptying of the machine can be carried out in complete isolation
and without product spreading into the environment. When using organic
solvents, the process machines can also be made inert and used with a solvent recovery system.
|
|
|
Principle of operation
With fluid bed coating, particles are fluidized and the coating fluid sprayed
on and dried. Small droplets and a low viscosity of the spray medium ensure an
even product coating.
Glatt offers Batch Fluid
Bed Systems in different batch sizes with:
Top Spray Coating
Bottom Spray Coating (Wurster
Coating)
Tangential Spray Coating (Rotor Pellet
Coating)
|
|
Principle: Batch fluid bed coating Top Spray |
Principle: Batch fluid bed coating Bottom Spray (Wurster
coating) |

Principle: Batch fluid bed coating Tangential Spray (Rotor pellet
coating) |
|
|
Glatt offers Continuous
Fluid Bed Systems for different throughputs with:
Top Spray Coating
Bottom Spray Coating
|
|
Principle: Fluid bed coating in the continuous Glatt fluid bed: Top
Spray
|
Principle: Fluid bed coating in the continuous Glatt fluid
bed: Bottom Spray |
|
|
Top Spray Coating
This process is used for general coatings right up to enteric
coating. With top spray coating in the fluid bed (batch and continuous),
particles are fluidized in the flow of heated air, which is introduced into the
product container via a base plate. The coating liquid is sprayed into the
fluid bed from above against the air flow (countercurrent) by means of a nozzle.
Drying takes place as the particles continue to move upwards in the air flow.
Small droplets and a low viscosity of the spray medium ensure that the
distribution is uniform.
Coating in the continuous fluid bed is particularly suitable for protective
coatings/colour coatings where the product throughput rates are high. The
product is continuously fed into one side of the machine and is transported
onwards via the sieve bottom by means of the air flow. Depending on the
application, the system is sub-divided into pre-heating zones, spray zones and
drying zones. The dry, coated particles are continuously extracted.
Bottom Spray Coating (Wurster coating)
This process is particularly suitable for a controlled release of active
ingredients. In the Wurster process, a complete sealing of the surface can be
achieved with a low usage of coating substance. The spray nozzle is fitted in
the base plate resulting in a spray pattern that is concurrent with the air
feed. By using a Wurster cylinder and a base plate with different perforations,
the particles to be coated are accelerated inside the Wurster tube and fed
through the spray cone concurrently. As the particles continue travelling
upwards, they dry and fall outside the Wurster tube back towards the base plate.
They are guided from the outside back to the inside of the tube where they are
once again accelerated by the spray. This produces an extremely even film.
Particles of different sizes are evenly coated.
Bottom Spray Coating (Continuous fluid bed)
Particularly suitable for protective coatings/colour coatings where the
product throughput rates are high. The product is continuously fed into one
side of the machine and is transported onwards via the sieve bottom by means of
the air flow. Depending on the application, the system is sub-divided into
pre-heating zones, spray zones and drying zones whereby spraying can take place
from below in the form of a bottom spray. The dry, coated particles are
continuously extracted.
Tangential Spray Coating (Rotor pellet coating)
Ideal for coatings with high solid content. The product is set into a
spiral motion by means of a rotating base plate, which has air fed into the
powder bed at its edge. The spray nozzle is arranged tangentially to the rotor
disc and also sprays concurrently into the powder bed. Very thick film layers
can be applied by means of the rotor method. See also -> Fluid Bed
Pelletizing
|
|
|
|
Process Principles
|
->Film Coating
->Lipid/Hotmelt Coating
|
|